Hot presses
Our hot presses are tailor-made systems with a hydraulic or electrical drive. They are used for the moulding and primary curing of powdery and simultaneously resin-impregnated friction lining materials such as brake linings and clutches under high temperatures and with long pressing times. The various system types are based on the required annual production capacity on the one hand and on the flexibility requirements on the other. All systems have a high degree of automation to enable constant and reproducible product quality. Through constantly optimised procedures in compression moulding, we offer our customers sophisticated solutions for automated system concepts.
Competitive advantage with
IAG Hot presses
- Very high technical availability
- Customer-specific design
- Long service life of the systems
- Low life-cycle costs with maximum quality
- Process-safe and stable
- Recipe-based product and production parameters
- Exact and central temperature control for low heat losses
- Hydraulic and/or electrical drive
- Ergonomic operation
- User-friendly interface
- Short tool-changing times and service-friendly design
- Flexible systems
- Customer-specific, fully interlinked production and manufacturing lines
Products

Rotary type machine
- Production of medium to large batches
- Customer-specific up to 5 handling stations
- Up to 19 presses
- Pressing force: 40-270 metric tons (to)
- Passenger vehicle, commercial vehicle or rail applications
- Cavities per tool: 1-8 (1/2/4/8)
- Tool temperature: usually 50-250°C
- Interlinking into a production centre is possible
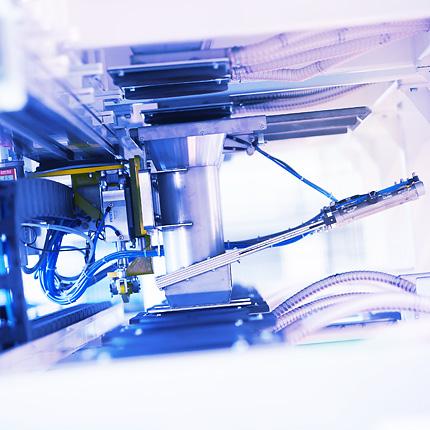
Linear Centre
- Production of small to medium-sized batches
- Highly flexible system
- Independent working of each press
- Individual lining type manufacture at each press
- Central electrical control and pressurised oil supply
- Up to 16 presses
- Pressing force: 40-270 metric tons (to)
- Passenger vehicle, commercial vehicle or rail applications
- Cavities per tool: 1-8 (1/2/4/8)
- Tool temperature: usually 50-250°C
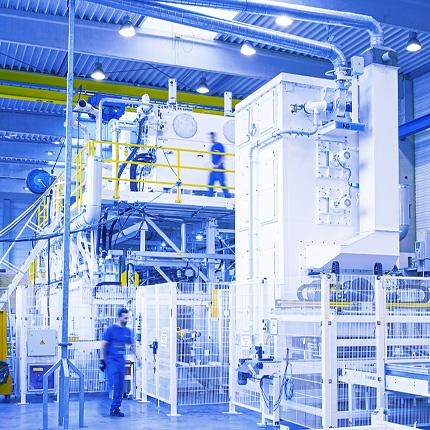
Eco Linear Centre
- Production of small to medium-sized batches
- Central magazine and shared manipulators
- Individual lining type manufacture at each press
- Central electrical control and pressurised oil supply
- Up to 16 presses
- Pressing force: 40-270 metric tons (to)
- Passenger vehicle, commercial vehicle or rail applications
- Cavities per tool: 1-8 (1/2/4/8)
- Tool temperature: usually 50-250 °C
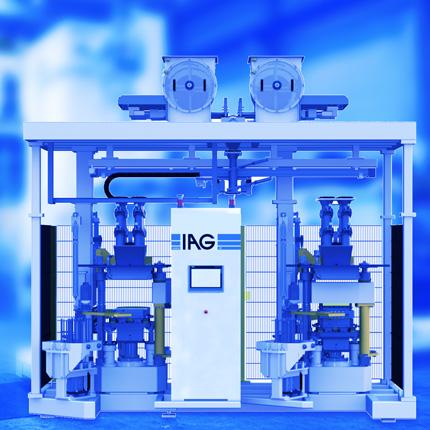
mLCx press
- Production of small to medium-sized batches
- 3 automation levels to choose from
- Short lead times/low installation costs
- Optimised assembly and logistics concept
- Plug’n’Play concept
- Passenger vehicle and/or commercial vehicle applications
- Universal servo distribution (programmable distribution curves)
- Module: 2x120to or 4x180to presses
- Multi-cavity concept with 1/2/4
- Tool temperature: usually 50-250°C